From Factory to Forest
Teamwork and pride go into every L-Series II machine
When we introduced our L-Series Skidders and Feller Bunchers four years ago, they redefined loggers’ expectations of what these machines could accomplish. Not content to rest on our laurels, we improved upon them with a simpler, easier-to-maintain design — our new L-Series II machines. We made improvements to over 1,600 parts, improved component placement, and dramatically reduced the complexity of the electrical and hydraulic systems.
And we continually refine them, based on invaluable input from loggers like you. We recently spoke with employees at the John Deere Davenport Works factory. Here’s an insider’s view of what they do to deliver machines that meet your needs — and stand up to whatever the forest throws your way.
The Worldwide Leader in Forestry
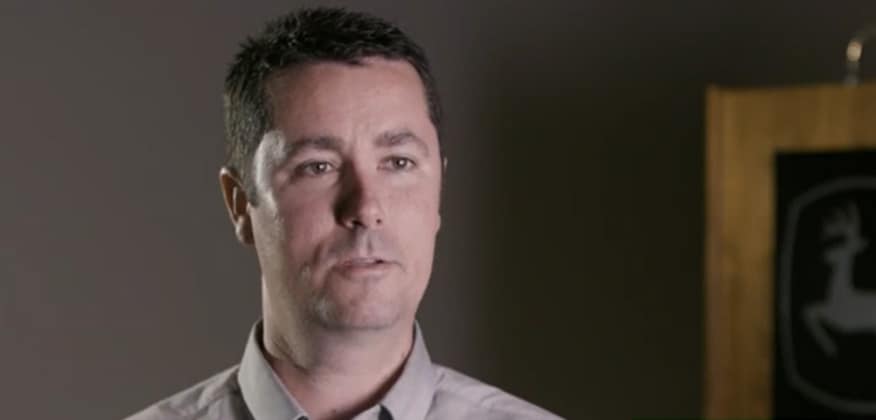
“John Deere is the worldwide leader in forestry, and we don’t take that for granted. We strive every day to meet our commitment to living up to loggers’ high expectations. The L-IIs were built on great things that came out of the L-Series, which provided a solid foundation to deliver exceptional uptime. Loggers work in rugged environments, and our goal is to produce machines that are bulletproof.”
John Hamilton
Program Manager, John Deere Forestry
Meeting Customer Needs
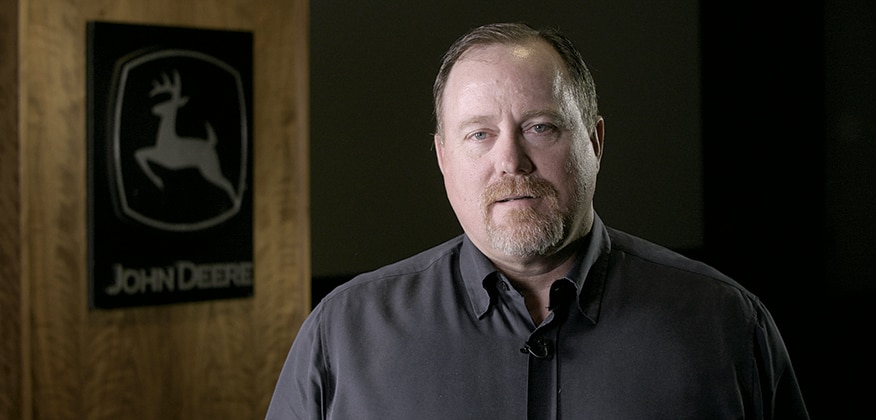
“The Enterprise Product Delivery Program (EPDP) for the L-IIs helps ensure that we’re meeting our customer requirements and addressing any performance gaps we might have had with the L-Series. The process is very detailed and includes virtual builds and actual builds of 11 machines that are rigorously tested in the woods. We’ve had excellent reports from the field on the quality of the L-IIs.”
Don Eckman
Business Unit Manager, Forestry Assembly
John Deere Davenport Works
Caring About Quality
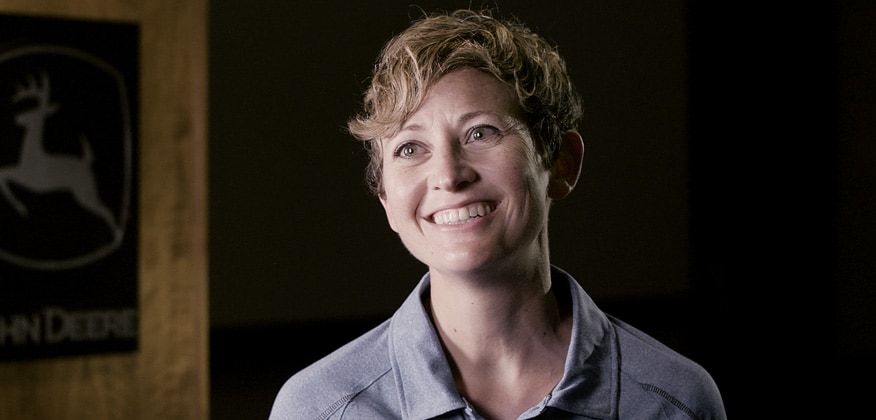
“The employees here at Davenport Works care a ton about quality. You can see how engaged they are when you walk around. People are wearing John Deere shirts. They smile, they wave, and they love meeting with customers. They are always talking about how we can do things better for the customer. It feels great to work with people like that every day.”
Mary Pat Tubb
General Manager, John Deere Davenport Works
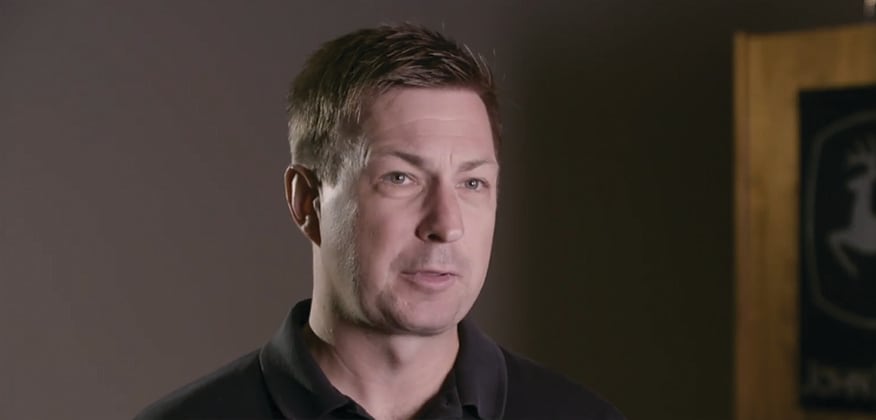
“We constantly strive to outperform customer expectations. Uptime is critically important to loggers, who work in adverse conditions. With the L-IIs, we made several improvements to servicing electrical and hydraulic systems, so they can get back up and running quickly.”
Chris Hoden
Operations Manager – Forestry
John Deere Dubuque Works
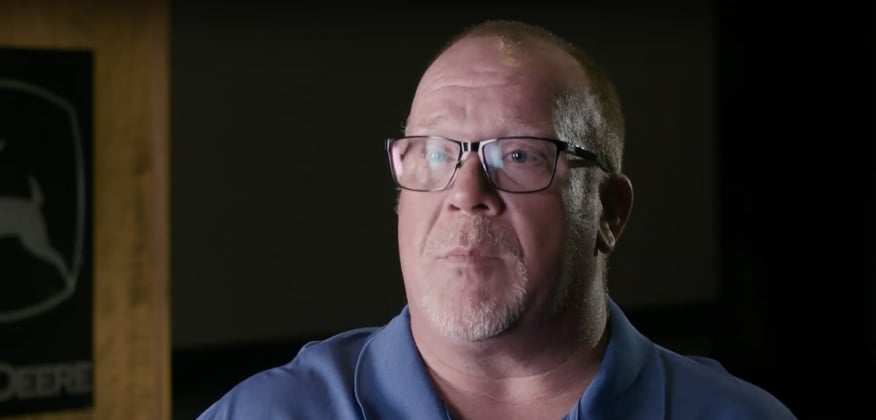
“Many of the improvements to the L-II machines came from my team on the line. For example, if the engine-frame harnesses are easier for us to install on the line, they’re going to be easier to service in the field. There’s never been an idea from one of our line people that wasn’t brought to the business unit managers or engineers to look at it for its feasibility.”
Todd O’Connell
Product Supervisor – Forestry
John Deere Davenport Works
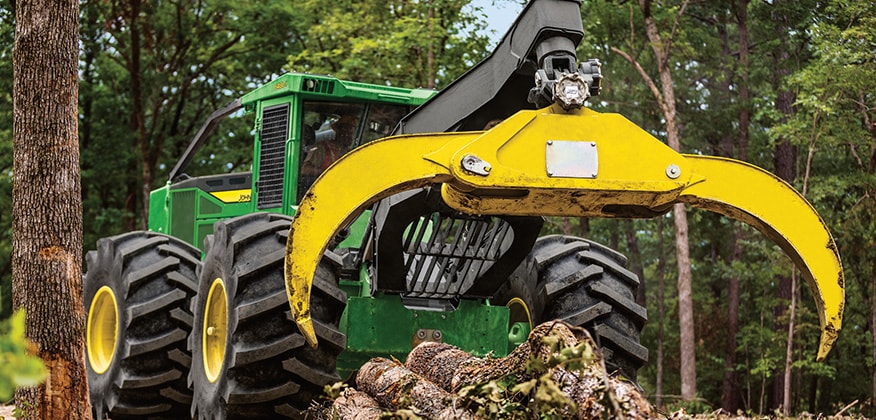
“We perform a verification audit to uncover any issue on the machine and fix it right away, so customers don’t experience the issue. We do extensive root cause analysis and put in steps to ensure the issue won’t happen again.”
John Hamilton
Program Manager, John Deere Forestry
Produced With Pride
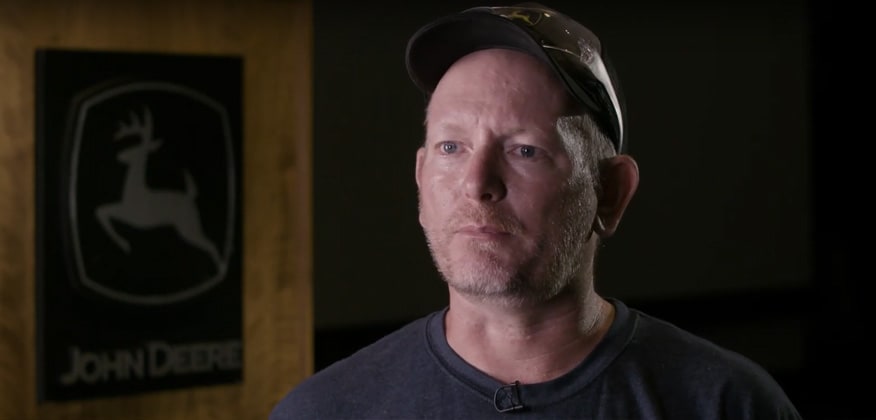
“When I build something, I pretend the guy I’m building it for is standing right next to me.”
Ryan Schneider
Assembler – Forestry
John Deere Davenport Works
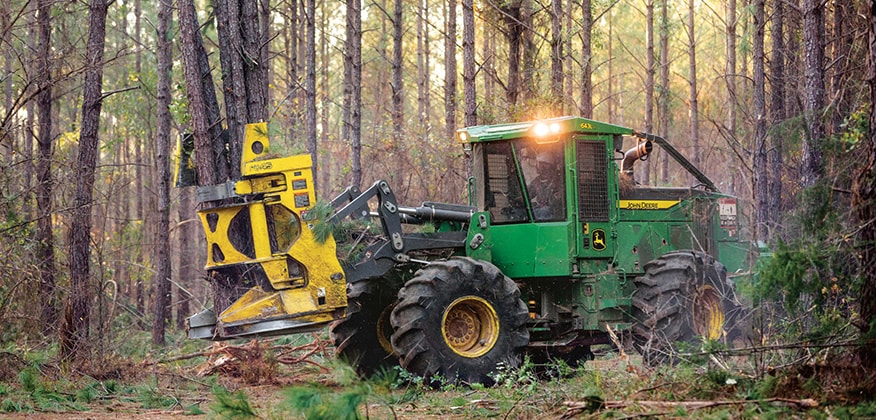
“Engaging our employees is at the heart of putting everything we have into our products every day. Their workmanship really delivers value and leads to success on the customer end. When we bring customers and dealers through the factory, they are most impressed by the level of involvement from the workers who actually build the products.”
Chris Hoden
Operations Manager – Forestry
John Deere Dubuque Works
Continually Evolving
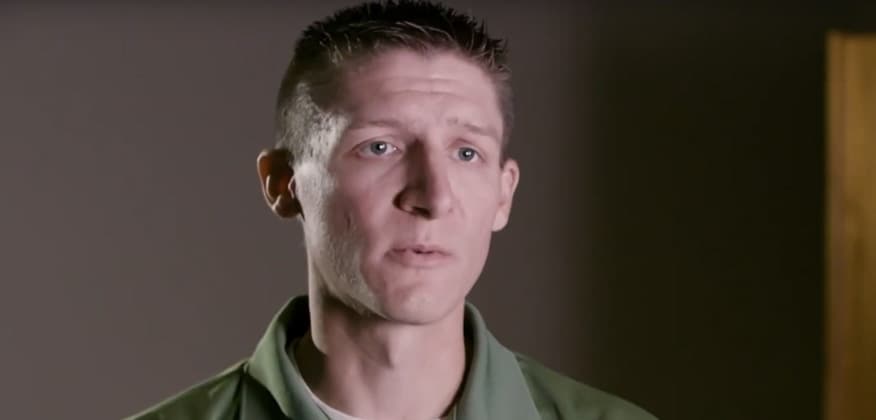
“The forestry industry is always changing, and John Deere is right on the cutting edge. Just as a logger must adapt to terrain, so do our products. We’re always looking at ways to improve and take our products to the next level.”
Dan Schelberger,
Customer Support Planner
John Deere Davenport Works
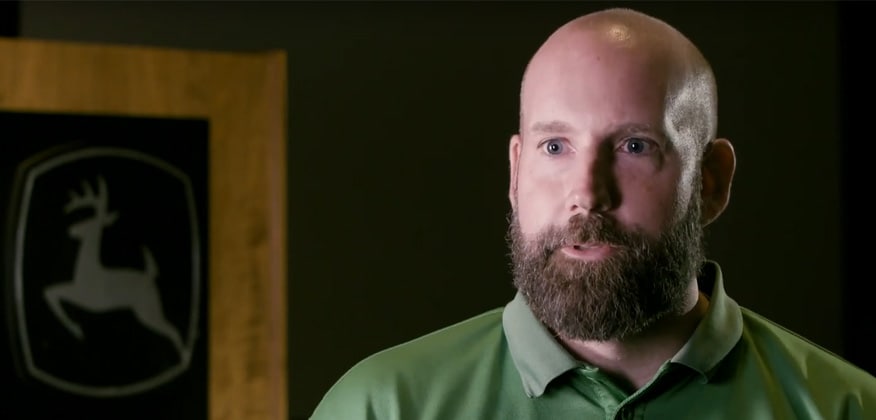
“We’re always here, tracking every warranty claim and working with dealerships to find better ways to make the machine. I personally read every single warranty claim that comes in to learn how we can improve our current product or the next revision of the machine. The best thing for me is for a customer to see a design change and say, ‘Man, that was really smart.’ That’s what keeps me coming to work every day.”
Jay Smith
Supervising Engineer, John Deere Dubuque Works