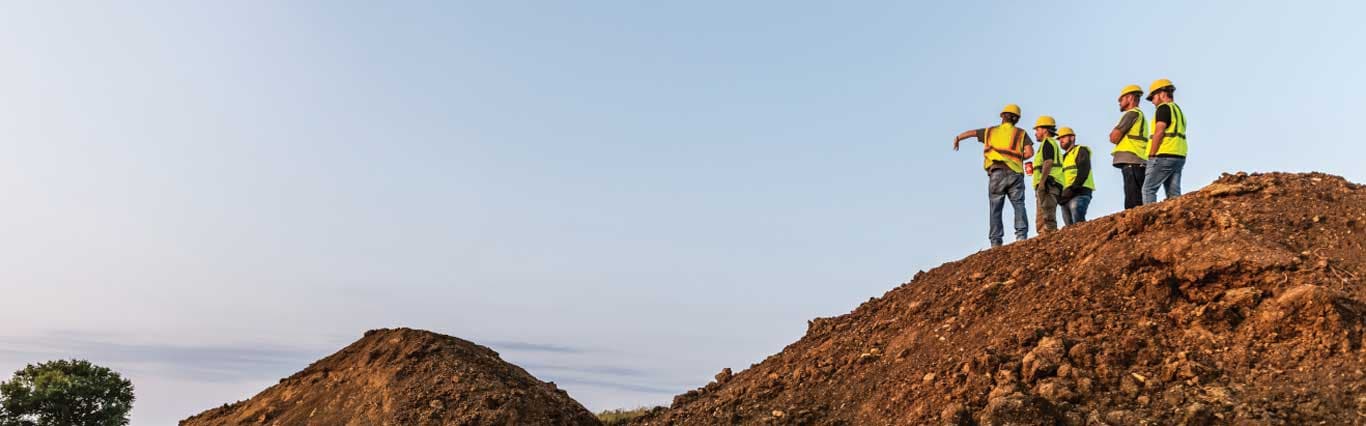
North Texas Crew Pushing Through the Dog Days of Summer
4 MIN READ
Sounding off about SmartDetect™
5 MIN READ
What drives the success of a Virginia company
5 MIN READ
Tag @JohnDeere on social media and show us where you have your Deere running.
Sent by Brittany L.
Sent by Jacob W.
Shared by Phil G.
Provided by Anonymous